In the high-stakes world of pharmaceutical QA/manufacturing, ensuring product quality and compliance is vital. However, the very processes designed to guarantee safety and efficacy are often slowed down by overwhelming documentation, manual reviews, and fragmented systems.
Quality Assurance (QA) teams find themselves dedicating approximately 30 percent of their time to documentation-related activities, including product dossiers, machine logs, batch records, and more, leaving little time for process improvement. [1] This creates bottlenecks, leading to delays in batch releases, increased risk of errors, and slow resolution of critical issues.
A single day of delay is worth approximately $800,000 in lost prescription drug or biologic sales. [2]
AI agents can now automate many of these manual tasks to address these challenges. By deploying SyncIQ’s state-of-the art "GMP Co-Pilot," companies can automate the most interpretation-heavy tasks that slow down manufacturing and QA workflows in pharma.
The Epicenter of Delay: Document, Review, and Compliance
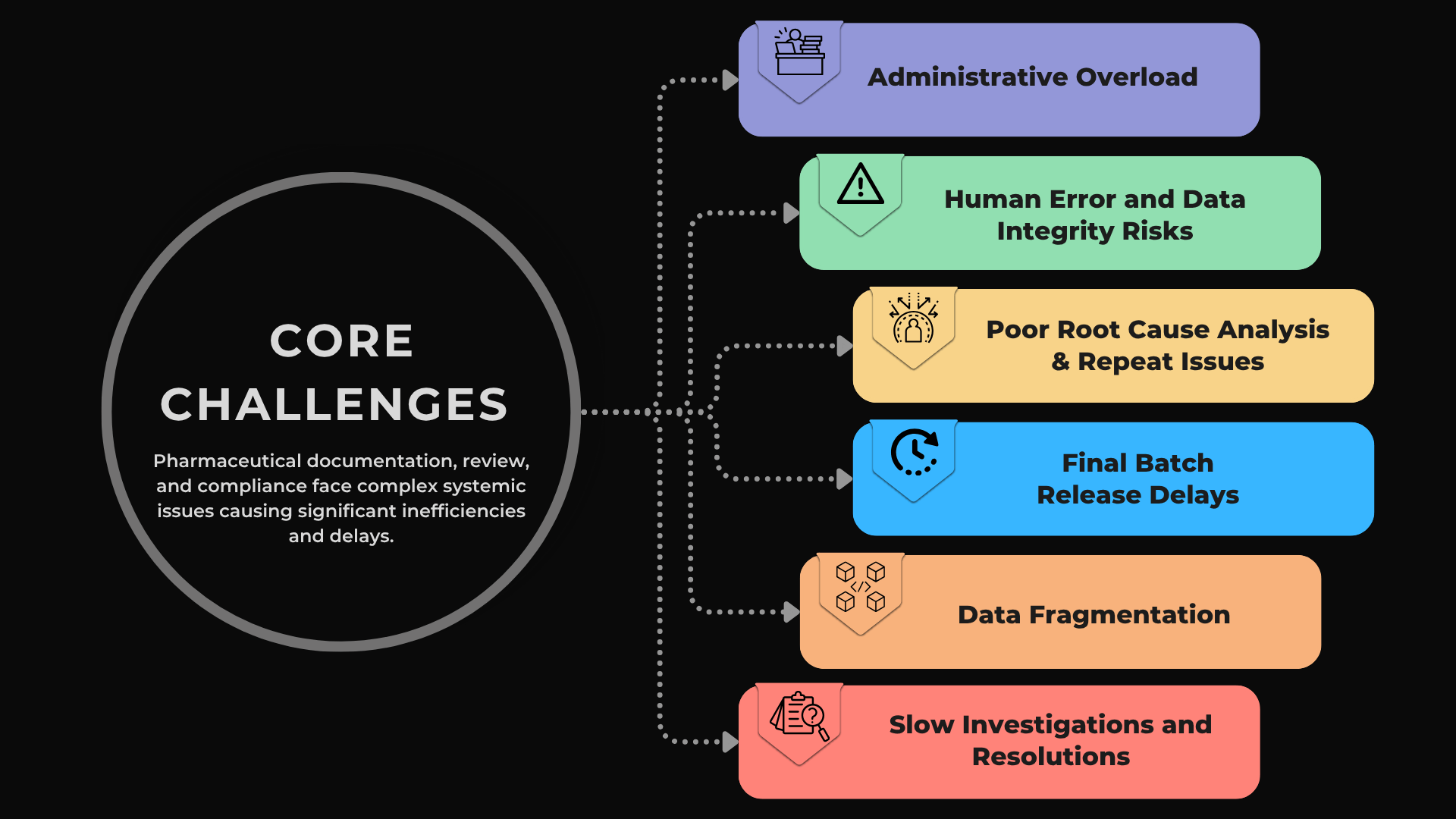
While the entire pharmaceutical manufacturing/QA lifecycle is complex, the processes centered around documentation, review and compliance are uniquely burdensome. This phase is filled with manual, repetitive, and error-prone tasks that create operational drag.
Let's take a look at some of the core challenges:
- Administrative Overload: QA teams are buried in manual reviews. Industry analyses show that quality assurance units can spend up to 80% of their time on review activities alone. [3] This time sink is a significant resource drain that shifts focus from strategic quality improvement to tedious administrative checking.
- Data Fragmentation: Critical data is scattered across disconnected systems like MES, LIMS, and ERP. QA personnel must manually hunt for, consolidate, and cross-reference information for every batch record, deviation, and CAPA. This not only slows down the entire process but increases the likelihood of critical oversights.
- High Risk of Human Error and Data Integrity Issues: Manual data transcription and verification are prone to error. A single misplaced decimal in a batch record containing anywhere from 5,000 to 45,000 manual entries can trigger a data integrity investigation, jeopardize a batch release, and attract regulatory scrutiny. [1]
- Slow Investigation and Resolution Cycles: The manual nature of investigations leads to crippling delays. The average time to close a single deviation investigation can range from 30 to 60 days. [4] This slow pace ties up expert resources, delays batch disposition, and leaves underlying process issues unresolved for extended periods.
- Poor Root Cause Analysis and Recurring Problems: Without data-driven tools, root cause analysis is often subjective and inconsistent, frequently failing to identify the true source of a problem. According to a study, organizations using traditional CAPA processes experienced a 16% repeat CAPA rate, meaning nearly 1 in 6 issues had to be addressed again, trapping organizations in a costly cycle of recurring deviations and wasted effort. [5]
- Final Batch Release Delays: Each of these challenges creates a compounding effect that creates a major bottleneck at the final release stage. Industry best practices often reference "right-first-time" (RFT) targets around 95% to enable efficient batch release. [6] But, organizations often struggle to achieve high RFT rates for documentation, which means means errors are often caught at the last possible moment, forcing costly rework and delaying patient access to critical medicines.
The SyncIQ Approach: Orchestrated AI Agents for Scaled Automation
SyncIQ's platform uses a team of specialized AI agents that work in concert to tackle these challenges at scale. These agents are designed to handle specific, context-heavy tasks within the documentation and review workflow, streamlining the entire process.
.png)
Key agents involved in this transformation include:
- Compliance Validation Agent: Automatically validates process parameters, signatures, and other entries within an EBMR against the defined rules in SOPs and MBRs, flagging any exceptions for human review.
- Deviation Categorization Agent: Swiftly classifies deviations by their type and severity based on predefined QA rules, allowing teams to prioritize their focus.
- Root Cause Analysis (RCA) Draft Agent: Accelerates investigations by generating structured RCA drafts using established methodologies like 5-Why or Fishbone, informed by historical data.
- CAPA Recommendation Agent: Suggests effective corrective and preventive actions by analyzing past deviations and the historical effectiveness of similar CAPAs.
- Report Generator Agent: Compiles all the necessary information into structured and consistent review summaries, deviation investigation reports, and CAPA documentation, preparing them for final QA approval.
By applying advanced analytics to quality management, one pharma company reduced deviations by more than 65% and uncovered hidden root causes of persistent issues that traditional methods had failed to detect. [Source: McKinsey & Company] [7]
Automated Workflows in Action
By orchestrating these agents, SyncIQ can help companies implement powerful automated solutions for their most significant Manufacturing/QA bottlenecks.
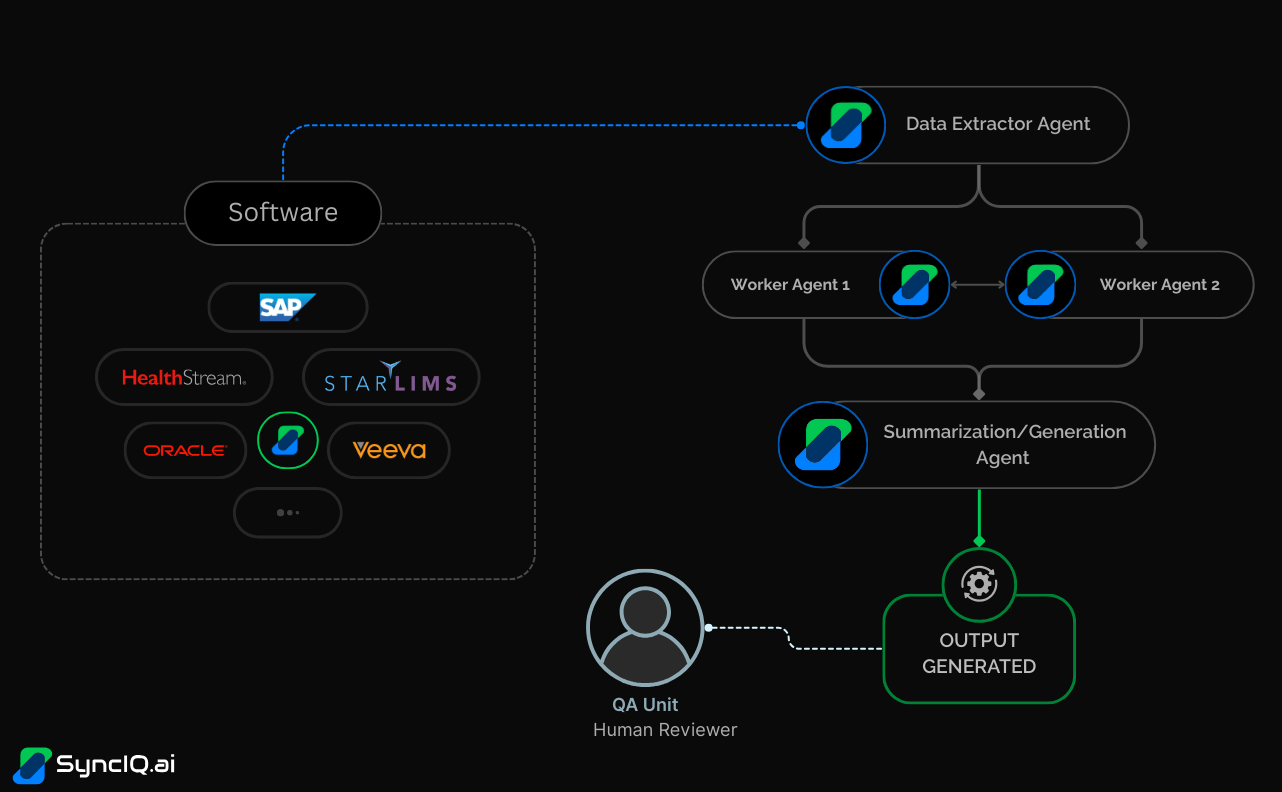
Now, let's take a closer look at how a QA/Manufacturing workflow could look like with SyncIQ's Agent-First approach:
- Input: The workflow begins when data is generated or required for review. This can be triggered by a new batch record, a deviation event, or the need for a periodic report, with agents interacting directly with legacy systems like SAP, Oracle, Veeva, StarLIMS, etc.
- Agent Actions:
- A Data Extractor Agent initiates the process by fetching and consolidating all relevant data from the various isolated software systems.
- A team of specialized Worker Agents then performs the core analytical work. This could involve validating data against compliance rules, categorizing an event, conducting a root cause analysis (RCA), or identifying historical trends.
- A Report Summarization/Generation Agent takes the findings from the worker agents and compiles them into a thorough, easy-to-follow draft document.
- Output: The automated process generates a comprehensive, pre-analyzed draft report or summary. This document is structured for clarity and highlights key findings, exceptions, and recommendations.
Human Review: The final output is delivered to the human QA expert. With the burdensome data gathering and initial analysis complete, the expert can focus their time on high-value tasks: verifying the AI-generated findings, applying their deep domain knowledge to the most critical issues, and making the final approval decision.
By using an Agent-First approach, SyncIQ can help pharmaceutical companies achieve more than 50% time saving in their QA processes, significantly improve compliance, and reduce the risk of costly errors and delays. They can then reallocate their most valuable resource—their human experts—away from tedious documentation and toward strategic process improvements and operational excellence.
References
[1] McKinsey & Company. (n.d.). Operations can launch the next blockbuster in pharma. https://www.mckinsey.com/capabilities/operations/our-insights/operations-can-launch-the-next-blockbuster-in-pharma
[2] Wright, T. (2024, September 5). Updates on the value of a day of delay in drug development. Contract Pharma. https://www.contractpharma.com/updates-on-the-value-of-a-day-of-delay-in-drug-development/
[3] McKinsey & Company. (n.d.). A new operating model for pharma: How the pandemic has influenced priorities. https://www.mckinsey.com/industries/life-sciences/our-insights/a-new-operating-model-for-pharma-how-the-pandemic-has-influenced-priorities
[4] BioProcess International. (n.d.). Transforming deviation management. https://www.bioprocessintl.com/risk-management/transforming-deviation-management
[5] MDIC. (2023, May). 2022 MDIC Make CAPA Cool Whitepaper. https://mdic.org/wp-content/uploads/2023/05/2022-MDIC-Make-CAPA-Cool-Whitepaper_v16.pdf
[6] BioPharm International. (n.d.). Streamlining batch record review and approval. https://www.biopharminternational.com/view/streamlining-batch-record-review-and-approval
[7] McKinsey & Company. (n.d.). Smart quality: Reimagining the way quality works. https://www.mckinsey.com/industries/life-sciences/our-insights/smart-quality-reimagining-the-way-quality-works